Linea AV Napoli Bari, cemento e calcestruzzo sostenibili per lo scavo iperbarico della galleria Casalnuovo
L'Italia si sta trasformando, e lo fa con un piano di ammodernamento senza precedenti attraverso lo sviluppo di diversi progetti infrastrutturali, finanziati o non finanziati dal Piano Nazionale di Ripresa e Resilienza (PNRR), che rispondono a una strategia di potenziamento della rete ferroviaria, soprattutto al Sud, fondamentale per realizzare un Paese sempre più interconnesso, capace di superare le diseguaglianze territoriali e migliorare la qualità dei servizi per i cittadini.
Sono oltre 30 le Opere Strategiche che rientrano nel piano. Tra queste, il potenziamento e la velocizzazione dell’itinerario Napoli - Bari che consentirà di integrare l’infrastruttura ferroviaria del Sud del Paese con il Core Corridor “Scandinavia - Mediterraneo”. Al termine dei lavori, i 145 km del collegamento Napoli - Bari saranno percorribili in 2 ore, contro le circa 4 attuali, ad una velocità massima di 250 km/h, mentre si impiegheranno soltanto 3 ore da Roma a Bari, con un risparmio di circa due ore rispetto ad oggi.
I lavori della linea AV/AC Napoli – Bari, iniziati tra il 2015 e il 2016, termineranno entro il 2028. Alcune tratte saranno attive già da prima, consentendo di ridurre – anche se parzialmente – la durata del tragitto.
Realizzare una linea ferroviaria che colleghi l’Italia da Est a Ovest non è semplice, perché significa attraversare le montagne degli Appennini, ma anche tratti di territorio fortemente urbanizzato. È il caso del lotto Napoli-Cancello, dove parte del tracciato passa sotto una linea ferroviaria preesistente, fattore che comporta l’esecuzione di scavi in profondità, fino a 13 mt sotto il piano di campagna, e la possibilità di interferenza con la falda acquifera. Nel dettaglio, è ciò che accade in un tratto della linea, quello della galleria artificiale Casalnuovo, che si sviluppa parzialmente sottofalda. Questo significa che, proprio dove viene scavata la galleria, la presenza dell’acqua è costante.
Qui, per la prima volta in Italia nell’ambito della costruzione di tunnel, si sta sfruttando lo scavo in modalità iperbarica, una tecnica innovativa per effettuare gli scavi in presenza di falda acquifera che prevede appunto il ricorso all’aria compressa per allontanare l’acqua dalle zone interessate. La pressione introdotta nel sito consente, infatti, di mantenere l’acqua al di sotto del fondo scavo, assicurando vantaggi anche dal punto di vista ambientale, senza i rischi associati all’uso di miscele cementizie che entrano in contatto con il terreno e la falda acquifera. Il particolare mix design del calcestruzzo necessario per la realizzazione del tratto di galleria in modalità iperbarica è stato progettato e fornito da Heidelberg Materials Italia Calcestruzzi Spa, (la storica Calcestruzzi Spa) che sta provvedendo anche alla fornitura del calcestruzzo impiegato nella realizzazione della galleria Casalnuovo (NA), per un quantitativo complessivo di circa 26 mila mc.
La metodologia di scavo iperbarico
La galleria Casalnuovo, lunga complessivamente 3.300 m, di cui 1.000 m già scavati con il precedente appalto IRICAV, è una galleria artificiale a doppia canna collocata in un sito di natura vulcanica piroclastica con media permeabilità (k 10-4÷10-5 m/s) e realizzata, per la maggior parte del suo sviluppo, tra paratie in diaframmi seguendo il “metodo Milano”. Per l’avanzamento dello scavo, il metodo in questione prevede una serie di fasi in successione: un prescavo di sbancamento, la realizzazione dei diaframmi in c.a. di paratie verticali e quindi della copertura con solettone in c.a., il ritombamento sulla copertura, lo scavo dall’interno del terreno compreso fra la copertura, le paratie verticali ed il piano di scavo ed infine la realizzazione delle strutture definitive interne in c.a., vale a dire delle fodere laterali e del solettone di fondazione. Quest’ultimo, avendo un’altezza eterogenea che in alcuni punti raggiunge e supera gli 80 cm, si configura come elemento di tipo massivo, per il cui getto, al fine di limitare l’insorgenza degli stati tensionali, che potrebbero dare origine ad uno stato fessurativo soprattutto nella fase di raffreddamento, è stato prescritto un calcestruzzo a bassissimo sviluppo di calore.
Nel tratto di galleria interessato dalla falda e realizzato in modalità iperbarica, lungo 650 m, è necessario assicurare una pressione costante, isolando l’intera area interessata dallo scavo. Per far questo, la tratta viene suddivisa in compartimenti stagni di circa 60 metri necessari per limitare le perdite di pressurizzazione e le infiltrazioni d’acqua di falda durante lo scavo, isolati l’uno dall’altro da diaframmi provvisori trasversali alla linea e abbattuti in successione con l’avanzamento degli scavi.
L’intervento, primo esempio in Italia di scavo sottofalda dopo rarissime realizzazioni in Europa, si configura come un’opera dall’alto impegno ingegneristico, innovativa e, allo stesso tempo, sostenibile. Nella tecnica di scavo in atmosfera iperbarica, infatti, l’utilizzo della pressione d’aria per mantenere l’acqua al di sotto del fondo scavo, non altera le condizioni del sottosuolo, lasciando l’acqua nel suo circolo naturale senza tuttavia fare in modo che possa venire a contatto con il calcestruzzo e additivi chimici e consentendo di lavorare in asciutto. Nei casi di scavo ordinari, in presenza di acqua, per contenerne le fuoriuscite si sarebbe dovuto utilizzare calcestruzzo impermeabile e resistente al dilavamento.
La pressione erogata in galleria oscilla tra 0,3 e 1,2 atmosfere, a seconda delle condizioni di lavoro. Ciò comporta che gli operai e gli addetti ai lavori debbano adattarsi alla differenza di pressione in una apposita camera di compensazione, che prevede una capienza massima di 20 operai che lavorano 24/7 su tre turni, nella quale avviene la fase di compressione graduale che dura in media 20 minuti. Tutte le attività si svolgono adottando procedure e specifici protocolli tecnici e sanitari che consentono di garantire la massima sicurezza e la salute degli operai durante le fasi di lavoro. Lungo i 650 metri dove viene applicata la tecnica dello scavo in atmosfera iperbarica il cantiere non si ferma mai, fino al completamento della galleria.
Il mix design del calcestruzzo
Per la realizzazione dello scavo iperbarico, i tecnici di Heidelberg Materials hanno progettato un calcestruzzo con un mix design particolare nel rispetto della classe di resistenza caratteristica progettuale, vale a dire Rck 30 in due varianti: la miscela C25/30 XC2 S5 D20 con impiego di cemento pozzolanico DURACEM IV/A (P) e il mix C25/30 XC2 S5 D10 è caratterizzato da basso calore di idratazione con utilizzo di cemento d’altoforno TERMOCEM III/A 32,5 R LH; per entrambi i mix è stato richiesto lungo tempo di mantenimento della lavorabilità e soprattutto alta pompabilità, dovendo il calcestruzzo essere trasferito fino ai punti di getto con l’attraversamento di centinaia di metri lineari di tubazioni.
Il calcestruzzo impiegato nel tratto di scavo iperbarico della galleria Casalnuovo viene fornito dall’impianto di betonaggio di Napoli Casalnuovo di Heidelberg Materials per un quantitativo stimato, ad oggi, superiore ai 10.000 mc.
Il mix-design è rappresentato da un calcestruzzo a prestazione garantita di classe di resistenza C25/30 progettato nel rispetto della norma europea UNI EN 206:2021 e nazionale UNI 11104:2016, verificata nella classe di esposizione ambientale di durabilità XC2 con rapporto a/c massimo di 0,60 e un contenuto minimo di cemento di 300 Kg/mc, in ottemperanza del Capitolato Generale Tecnico di Appalto (CGTA).
“Il soddisfacimento della specifica esigenza di pompabilità, ha richiesto un calcestruzzo fluido. Fondamentale, a tal fine, è la classe di consistenza di progetto del calcestruzzo che mira all’ottenimento di uno Slump Test corrispondente all’S5, quindi un calcestruzzo dalla reologia fluida al limite con la caratteristica propria di un Self Compacting Concrete (SCC) e un massimo valore di abbassamento al cono di Abrams accettato al momento della verifica in cantiere ≤ 250 mm (rif. CGTA)”, spiega Luciano Padalino, Responsabile del Servizio Tecnologico Territoriale Area Sud di Heidelberg Materials Italia Calcestruzzi Spa. La verifica della conformità alle specifiche di progetto della classe di consistenza del calcestruzzo si determina mediante il metodo del cono di Abrams (Slump-Test), che vede lo sfilamento dello stampo tronco-conico seguito dalla misurazione in millimetri (Slump Test) dell’abbassamento del calcestruzzo fresco rispetto all’altezza del cono. La conoscenza di tale parametro è di fondamentale importanza per la definizione della lavorabilità del calcestruzzo.
“Per conferire specifica fluidità all’impasto, necessaria per agevolare lo scorrimento all’interno delle tubazioni distribuite fino al punto di getto per centinaia di metri, la struttura composizionale della miscela, nella versione dell’impiego del diametro massimo 10 mm (Dmax 10 mm), è caratterizzata dalla quantità di finissimi, contenuti fra i 500 e 600 Kg/mc, parametro questo che caratterizza i calcestruzzi SCC.
L’inserimento di filler calcareo nel mix design, nella misura di 120 kg/mc, consentirà alla miscela di calcestruzzo di superare il salto di quota di circa 10 metri rispetto al piano di campagna e di proseguire la sua corsa mantenendo invariata la sua plasticità per più di 250 metri lineari, distanza alla quale, fino ad oggi, è stato necessario pompare il calcestruzzo con sistemi pneumatici di compressione. I finissimi conferiscono alla miscela proprietà reologiche che riducono, quasi annullano, l’attrito con le pareti delle tubazioni conferendo scorrevolezza all’impasto che giunto al punto di getto si presenta coeso e facilmente lavorabile per una corretta costipazione eseguita a regola d’arte”, aggiunge Padalino.
Le due miscele (Dmax 20 e Dmax 10 mm) sono state studiate per mantenere la reologia iniziale, registrata a 10 minuti, fino a un massimo di 90 minuti, come richiesto dalla Stazione Appaltante ITALFERR. “Queste caratteristiche – precisa Padalino - sono state garantite impiegando additivi acrilici di nuova generazione ai quali è stato associato un additivo specifico estensore della lavorabilità che, appunto, garantisce la stessa lavorabilità a tempi prolungati e a temperature ambientali severe, come quelle del periodo estivo”.
I cementi utilizzati per il confezionamento della miscela iperbarica
Al fine di ridurre e contenere il calore sviluppato dal calcestruzzo in fase di presa per opere ritenute massive, è stato richiesto, per determinate parti della struttura, un cemento specifico che in fase di idratazione sviluppasse meno elementi chimici, come il cemento d’altoforno. Per il confezionamento del calcestruzzo - “miscela iperbarica C25/30 XC2 S5 D10” - è stato utilizzato il cemento CEM III/A TERMOCEM GREEN 32,5R - LH (LOW HEAT) di Heidelberg Materials prodotto presso lo stabilimento di Castrovillari, che utilizza il clinker prodotto dalla cementeria di Matera, certificata in conformità alle norme ISO 9001 e ISO 14001 e, a maggio 2022, secondo lo schema internazionale CSC (già RSS) del Concrete Sustainability Council. Questo cemento appartiene al nuovo brand globale di prodotti evoBuild, la nuova gamma di cementi e calcestruzzi sostenibili di Heidelberg Materials sviluppati per ridurre l'impatto ambientale e migliorare l'efficienza dei progetti di costruzione. La gamma evoBuild è caratterizzata da cemento e calcestruzzo a basse emissioni di CO₂, contenenti materiali da riciclo (nel calcestruzzo) oppure entrambe queste due caratteristiche.
“Il TERMOCEM GREEN 32,5 R – LH è un cemento di altoforno con un contenuto di materiale di riciclo pre-consumo superiore al 30% ed è prodotto con emissioni di CO2 (Core Processes) inferiori a 550 kg/t contro un dato di oltre 750 kg/t per un CEM I”.
Conformemente alla composizione prescritta dalla norma UNI EN 197-1, questo cemento d’altoforno tipo III ad alta resistenza (classe 32,5), contiene il 35 – 64% di clinker ed è caratterizzato da un elevato tenore di materiale riciclato 36 - 65% di loppa granulata di altoforno e dallo 0 - 5% di costituenti minori.
“Il cemento in questione consente di produrre calcestruzzi di elevata durabilità. Infatti, il contenuto di loppa granulata di altoforno (36-65%), materiale di riciclo di pre-consumo proveniente dagli altoforni di lavorazione del minerale ferroso, contribuisce a conferire al calcestruzzo una resistenza agli ambienti moderatamente aggressivi (presenza di cloruri, acque moderatamente solfatiche e dilavanti, contatto con gliceridi), spiega Deborah Floris, Direttrice Area Centro di Heidelberg Materials Italia Calcestruzzi.
Inoltre, il basso calore di idratazione facilita l’esecuzione di getti in calcestruzzo di elevato spessore riducendo il rischio di fessurazioni termiche; per questo, il TERMOCEM 32,5 R – LH GREEN è indicato ove viene richiesto un cemento a basso calore di idratazione (LOW HEAT cement)”, afferma Padalino.
Infine, il cemento TERMOCEM GREEN 32,5 R – LH contribuisce all’ottenimento di punti su alcuni criteri dei sistemi di certificazione LEED (Leadership in Energy and Environmental Design) e CAM (Criteri Ambientali Minimi) nelle analisi multicriteri per la valutazione della sostenibilità ambientale degli edifici secondo il protocollo ITACA (Innovazione e Trasparenza degli Appalti e la Compatibilità Ambientale).
L'altro prodotto utilizzato, il cemento pozzolanico DURACEM CEM IV/A(P) 42,5 R-SR a.r.s. (proveniente dalla cementeria di Colleferro a sud di Roma), è anch’esso caratterizzato dalla presenza ridotta di clinker, se confrontato con ordinario cemento Portland, ha risposto bene in termini di sviluppo di calore per quota-parte composto da pozzolana naturale.
Il contenuto di costituenti a comportamento pozzolanico (pozzolana naturale) tra 11% e 35% è inoltre in grado di conferire al prodotto una resistenza agli attacchi chimici. In funzione della classificazione, è particolarmente indicato per opere esposte ad ambienti soggetti ad aggressione da solfati oltre che da solubilizzazione di acque dilavanti e cloruri. La resistenza ai solfati è assicurata dalla classificazione “SR” secondo la UNI EN 197-1 e “ars” secondo la UNI 9156.
Un cantiere d’eccellenza per portare l’alta velocità in Puglia
La galleria di Casalnuovo è parte di un’opera complessa e strategica per l’intero Sud Italia. Il lotto Napoli-Cancello rientra infatti in uno dei 4 lotti (Napoli-Cancello, Napoli-Hirpinia, Hirpinia-Orsara, Orsara-Bovino) della AV/AC Napoli-Bari che RFI sta realizzando con l’obiettivo principale di velocizzare il collegamento attuale e migliorare l’accessibilità al servizio nelle aree attraversate, sia per servizi nazionali di lunga percorrenza, sia per il servizio regionale e merci. Nel complesso si tratta di 74 chilometri di linea ad alta velocità/alta capacità, 10 viadotti e 6 tra nuove stazioni e fermate e 6 gallerie per la cui realizzazione è previsto l’impiego di 8 grandi talpe meccaniche.
L’opera rappresenta un grande volano per la creazione di posti di lavoro. Dal progetto sono impegnate oltre 7 mila persone, tra ingegneri, tecnici e operai. Un progetto ambizioso perché innovativo, sicuro, sostenibile e anche profondamente rivoluzionario per il territorio che interessa. La linea AV/AC Napoli-Bari consentirà non solo di collegare il Paese sul versante Est/Ovest ma porterà anche notevoli benefici anche in termini di sostenibilità ambientale, consentendo di evitare oltre 3 milioni di t di emissioni di CO2 nel periodo 2023-2047.
Heidelberg Materials è parte di questo grande progetto. Forte di expertise e competenze maturate negli anni nella capacità di offrire soluzioni su misura per i propri clienti, è in grado di fornire cementi e calcestruzzi che uniscono alla qualità, l’affidabilità e la durabilità di sempre, requisiti di sostenibilità, distinguendosi per lo speciale contributo alla riduzione della CO2 e per la circolarità dei propri prodotti. Con i cementi e i calcestruzzi della gamma evoBuild continua l’impegno del Gruppo nella riduzione dell’impatto ambientale dei propri prodotti e di qualsiasi progetto edile nei quali essi vengano impiegati, nel percorso verso il net zero al 2050.
Dati tecnici del cantiere
• Cantiere: Appalto per l’esecuzione della progettazione esecutiva e dei lavori della linea ferroviaria Napoli-Bari – tratta – Napoli-Cancello in variante tra le pk.0+000 (coincidente con pk 241+7272 della LS) e pk. 15+585 (coincidente con il km 229+530 della LS) incluse opere accessorie, nell’ambito degli interventi di cui al D.L. 133/2014, convertito in legge 164/2014 (c.d. “Sblocca Italia”) Convenzione n°5 del 18/12/2017
• Stazione Appaltante e Collaudo: Italferr SpA
• Contraente Generale: RFI – Rete Ferroviaria Italiana SpA
• Direzione di Cantiere ed Esecutori dei Lavori: R.T.I. composta da Webuild (Mandataria) e Partecipazioni Italia (Mandante)
• Impresa: NACAV S.c.a.r.l.
Posizione
(Italia)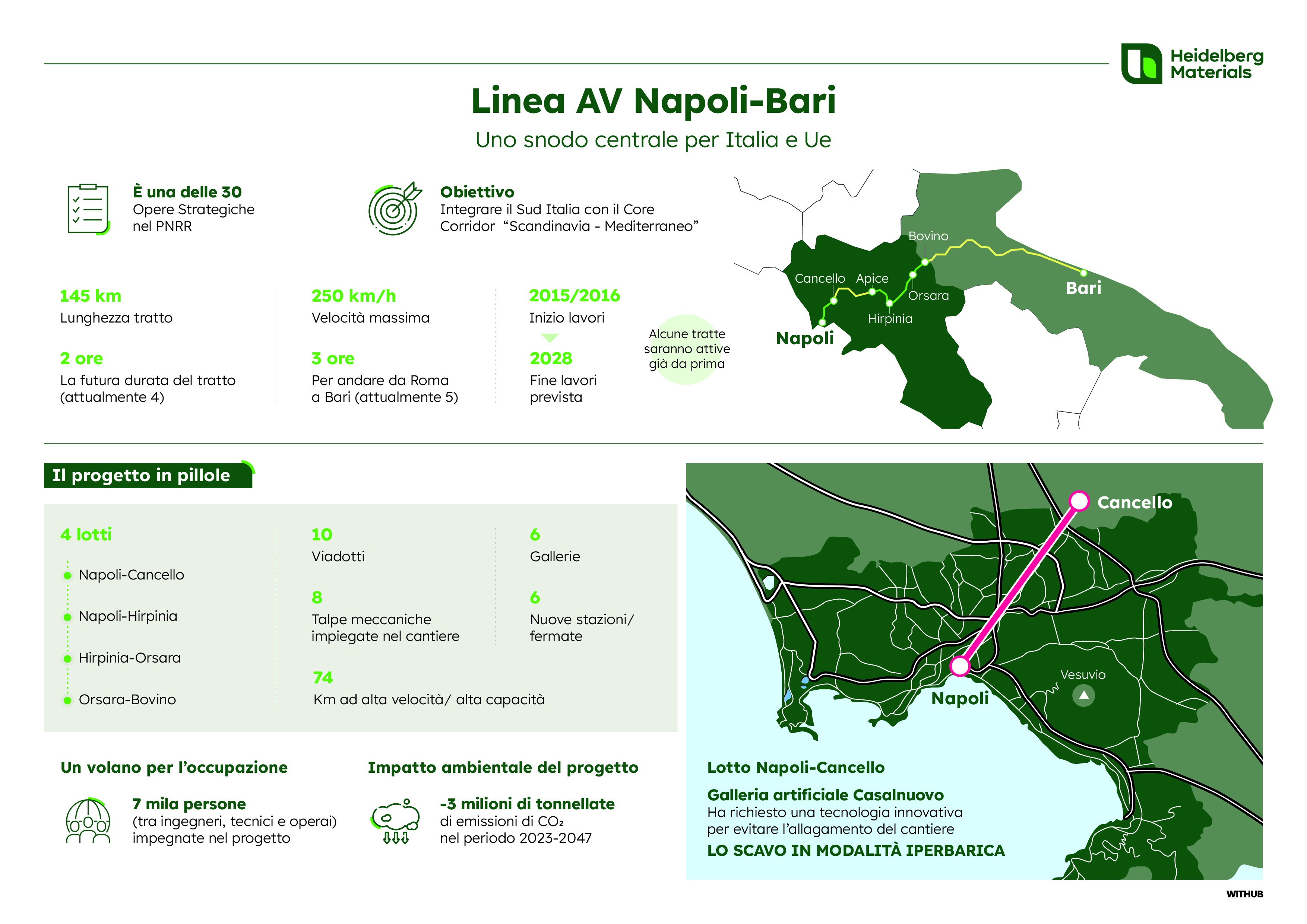
HM ITALIA_GalleriaArtificiale_Tavola01.jpg.
Heidelberg Materials Italia
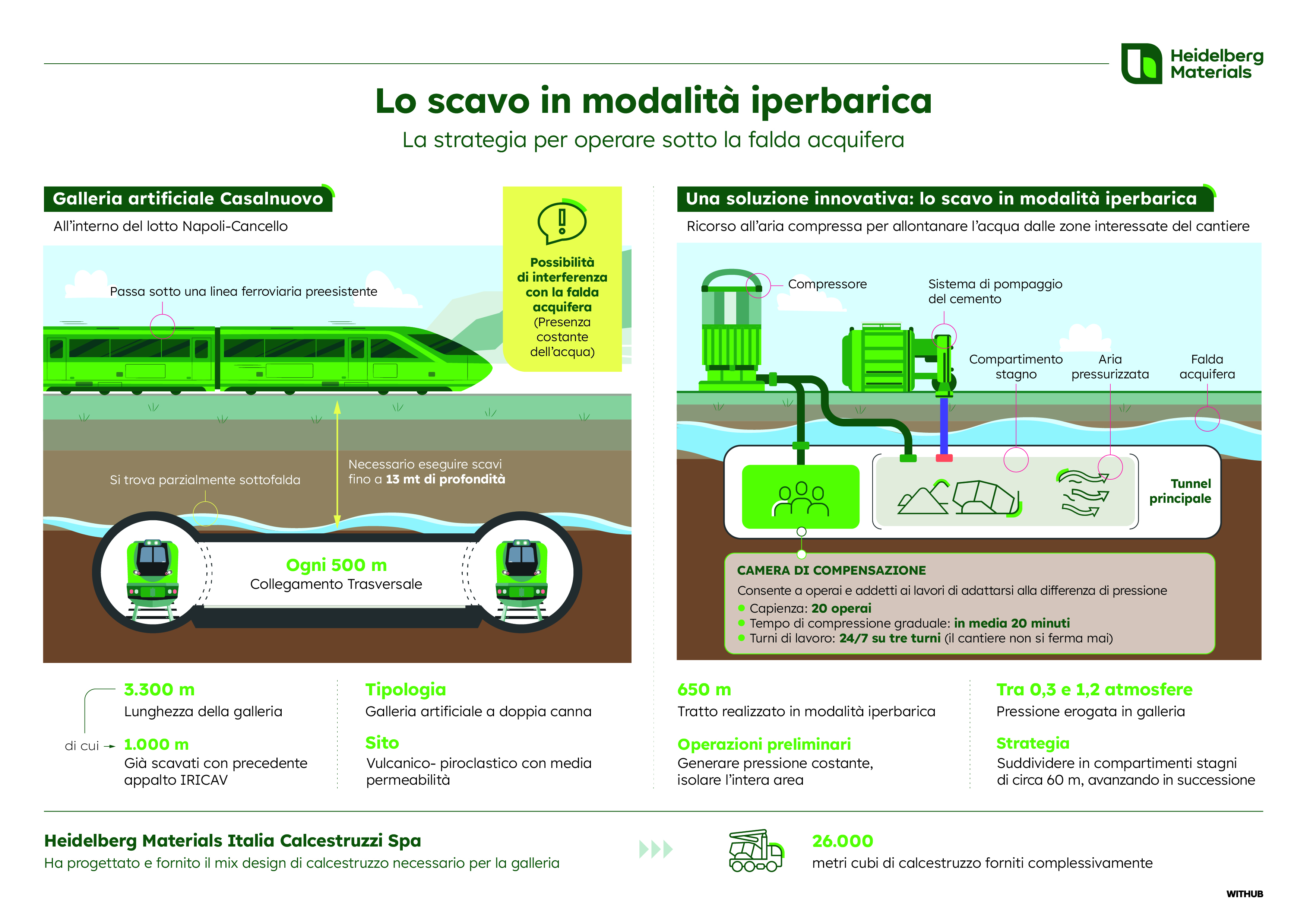
HM Italia_GalleriaArtificiale_Tavola02.jpg.
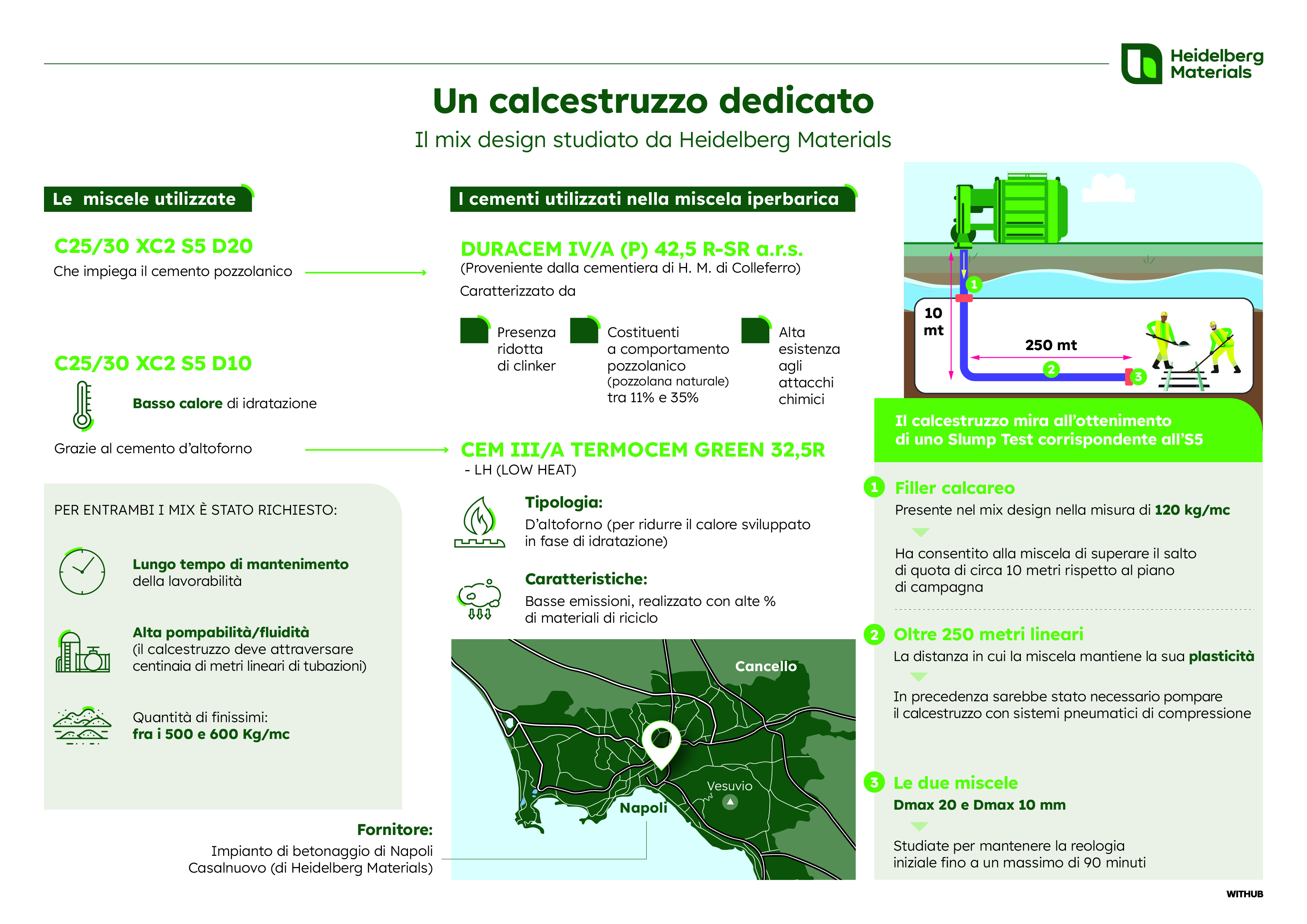
HM Italiai_Galleria Artificiale_Tavola03.jpg.
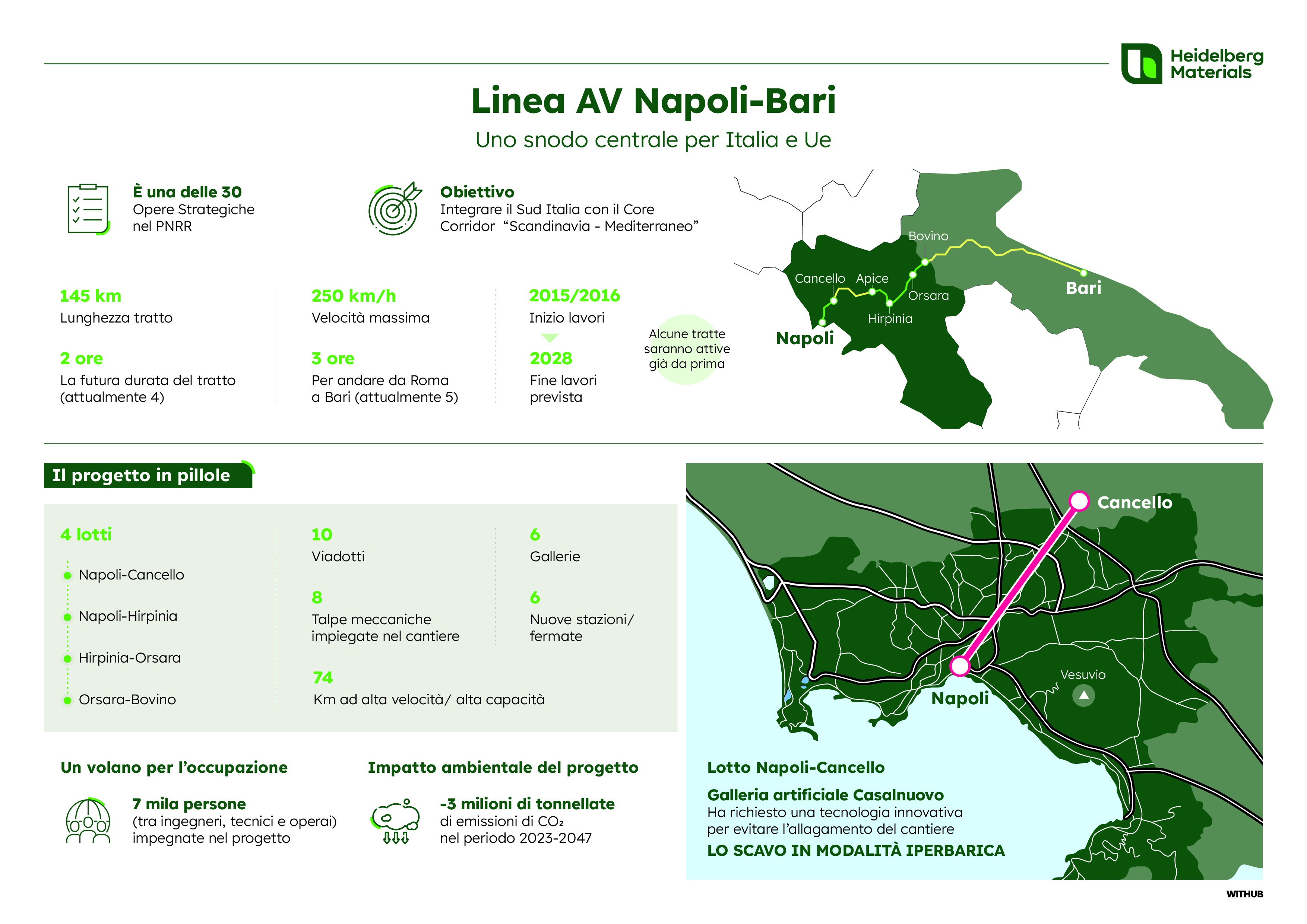
HM ITALIA_GalleriaArtificiale_Tavola01.jpg.
Heidelberg Materials Italia
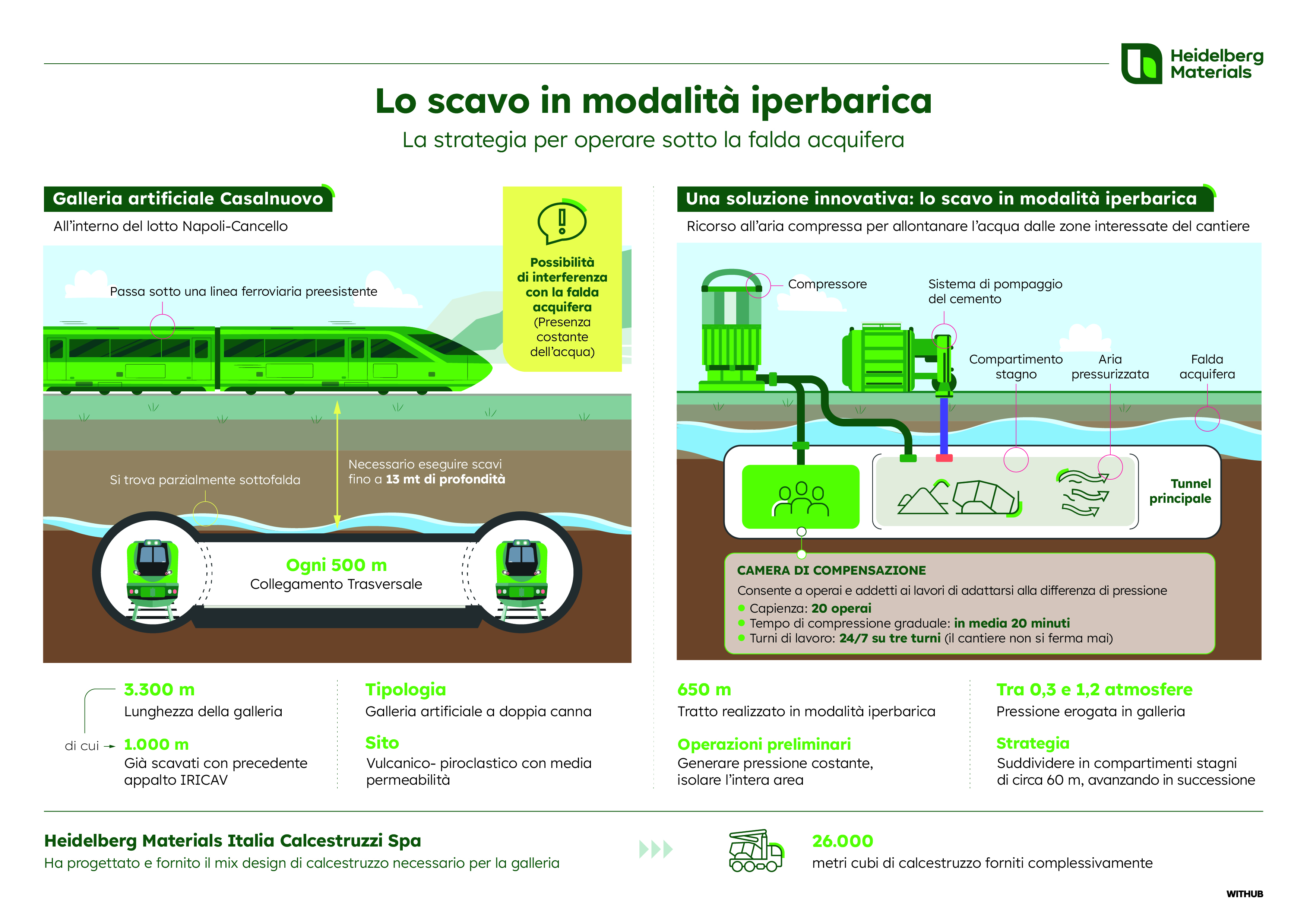
HM Italia_GalleriaArtificiale_Tavola02.jpg.
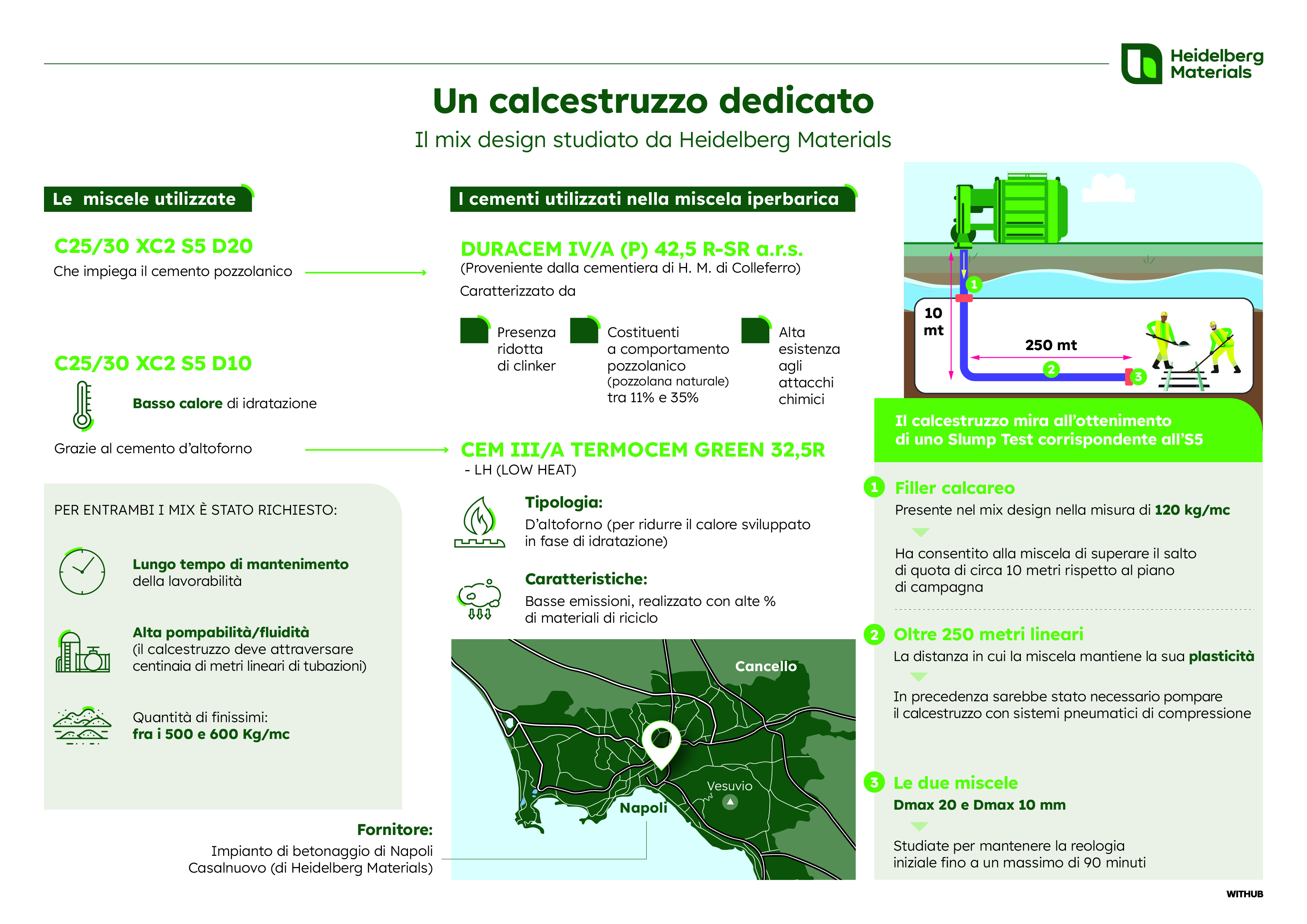
HM Italiai_Galleria Artificiale_Tavola03.jpg.