Il campanile di Majano (UD): quando costruire diventa un'arte
Il calcestruzzo è un materiale vivo, sempre pronti ad adeguarsi a tecnologie costruttive di ultima generazione. E il campanile di Majano (Ud) ne è una testimonianza concreta dove architettura, ricerca, innovazione e sostenibilità si fondono in un’unica realizzazione. Distrutto da sisma del Friuli del 1976 è stato ricostruito sul basamento della vecchia torre campanaria della chiesa parrocchiale e inaugurato nel maggio 2012. Una struttura di tale prestigio architettonico e significato simbolico imponeva l’impiego di un calcestruzzo straordinario, capace non solo di prestazione meccanica e durevolezza di rilievo, ma caratterizzato anche da un colore bianco di notevole brillanza e dal potere di conservare inalterato nel tempo l’aspetto estetico grazie alla proprietà dell’auto-pulizia della superficie Per questo motivo è stato utilizzato calcestruzzo i.active TECNO contenente TX Active il principio attivo fotocatalitico per materiali cementizi già apprezzato dal mondo delle costruzioni, brevettato da Italcementi. Il prodotto utilizzato a Majano è stato messo a punto, attraverso diverse prove di laboratorio, da Calcestruzzi e testimonia la capacità della società di tradurre in prodotti e soluzioni concrete, i progetti per il territorio e la comunità.
Quello che a prima vista potrebbe sembrare un mero esercizio stilistico costituito da una struttura monolitica in calcestruzzo inclinata su un lato, al suo interno racchiude un caleidoscopio di forme e di volumi che si intersecano per l’intera altezza a definire quasi una scultura equilibrata di vuoti e pieni. Il calcestruzzo, materiale con proprietà eccezionali, che permette di essere plasmato secondo forme diverse trova in questa struttura la sua piena espressione concedendosi in superfici piane, curve, spirali, unendosi in rastremazioni tra elementi verticali, orizzontali ed inclinati. Non solo, ma esigenze architettoniche hanno portato all’adozione di un conglomerato cementizio innovativo con prestazioni elevate e caratteristiche autopulenti, messo a punto da Italcementi, il TX Active già utilizzato in strutture architettoniche di pregio e in grado di abbattere gli agenti inquinanti. La sua cromaticità inoltre è doppia: da una parte legata al tradizionale grigio, mentre dall’altra ad un candido bianco entrambe miscelati a polveri ed inerti nobili derivanti dalla macinazione di marmi bianchi e sabbie silicee. Pochi i riferimenti fissi su quelli che sono i 43 metri di altezza: un solo spigolo interno che si sviluppa in verticale a tutta altezza sulle due vele bianche, e due fili fissi di un imponente cilindro grigio anteriore il resto sono murature che si arrampicano con inclinazioni diverse, rampe di scale a dimensione variabile ed un nocciolo interno che cambia forma ben 4 volte prima di arrivare alla cella campanaria. Tutto ciò si traduce in un grado di difficoltà elevato che può essere risolto solamente con maestranze altamente specializzate, coadiuvate da tecnici preparati che uniti ad una flessibilità realizzativa ad una continua ricerca nella ottimizzazione dei materiali hanno saputo realizzare casseri e carpenterie di volta in volta ridisegnate e modificate a seconda delle esigenze. La chiave di svolta è stata nell’individuare un programma di getti con una sequenza ben precisa degli stessi che permettesse la realizzazione delle fasi lavorative di casseratura, getto e scassero senza incappare in situazioni dalle quali non si potesse uscire se non con parziali demolizioni o con giunti di ripresa in posizioni strategiche non definite a priori. Programmazione basata oltre che su variabili di tipo realizzativo, anche su altre come la consistenza del materiale che passava da S3 all’S5 all’autocompattante a seconda dell’impiego su scale pareti o solette, per cui si presupponeva l’adozione di additivi fluidificanti differenti per quantità e tipologia opportunamente testati con largo anticipo in laboratorio, modificando successivamente in cantiere le ricette per ottimizzare la lavorabilità e la resa in base alle diverse differenze climatiche ed atmosferiche che si venivano a creare nel corso dei getti. Altra variabile da considerare è stata la messa in opera che ha portato all’adozione di autopompe di dimensioni variabili, con sviluppi dalla piccola 28ml sino alla enorme 58ml a seconda delle altezze e della posizione di getto. Dove le tubazioni e quest’ultime non arrivavano si è dovuto usare la benna con bocca a tubo al fine di evitare salti di quota importanti al calcestruzzo in fase di messa in opera che potessero comportare una segregazione dello stesso. Come si può ben immaginare l’adozione di un sistema piuttosto che dell’altro, unito alla variabilità delle condizioni climatiche, definisce fluidità e tempi realizzativi diversi che presuppongono miscele che venivano assestate e corrette di volta in volta in diversi momenti nel corso dello stesso getto. Un programma quindi che si è sviluppato in diverse fasi altalenando grigio e bianco consistenze e granulometrie differenti e aprendo nuove problematiche derivanti dall’instabilità verticale degli elementi estremamente snelli e non collegati tra di loro da orizzontamenti che hanno necessitato l’adozione di puntoni di contrafforte capaci di far collaborare gli stessi evitando possibili collassamenti della struttura. Lo speciale calcestruzzo ha portato anche all’adozione di armature particolari con un acciaio zincato ed ad un sistema di ripresa a “boccole” che ha ottenuto la certificazione proprio in questo cantiere. Lo stesso è caratterizzato da tondini opportunamente sagomati con alle estremità delle barre filettate che venivano fissate con estrema precisione nel getto, protette con polistirene e una volta scasserato e liberate dallo stesso si applicava avvitando con chiave dinamometrica la relativa ripresa di getto. Sistema pratico efficace ma, non sempre facile da realizzare vista la quantità e la disposizione dell’armatura presente, in virtù del fatto che la posizione delle stesse doveva essere estremamente precisa rispettando anche un copriferro minimo di 35mm. Inoltre per l’intero sviluppo della tromba delle scale, la realizzazione di quello che a tutti gli effetti è un pilastro mezzo grigio e mezzo bianco, ha portato all’adozione di un altro sistema di ripresa costituito da ancoraggio del tipo chimico mediante resine certificate secondo la nuova normativa sismica con la realizzazione di imperniature con diametri e passi variabili. Il tutto assemblato in opera come da progetto con distanziali, legature, cerchiature, infittimenti e sovrapposizioni così come prevede la corretta realizzazioni in zona sismica. Il sistema di avanzamento nei getti è stato effettuato sposando la soluzione degli impalcati rampanti che si inerpicano in verticale con il fissaggio tramite asole a dei bulloni esterni il cui alloggio veniva per tempo disposto nel getto precedente a misure predeterminate. A queste piattaforme poi venivano appoggiate verticalmente le pannellature di cassero capaci di traslare in senso orizzontale mediante binari, regolate in altezza con viti senza fine accostati tra di loro e opportunamente sigillati con opportuni siliconi acrilici per avere una perfetta tenuta del getto. Le difficoltà in questo caso oltre alla movimentazione e al corretto posizionamento in quota di elementi di notevole dimensione e peso erano rappresentate dai cedimenti in senso verticale della struttura man mano che veniva caricata dai pannelli di cassero, rendendosi necessaria una continua regolazione degli stessi. Inoltre in sede di getto le enormi spinte presenti portavano ad un continuo seppur minimo assestamento della struttura di contenimento che doveva essere continuamente monitorata al fine di mantenere il corretto piombo e squadro. La necessità di ottenere delle superfici di getto dall’aspetto marmoreo estremamente lucide hanno fatto si che i casseri dovessero essere rivestiti da un particolare compensato multistrato, con un rivestimento superficiale sintetico a base di vetroresina estremamente liscio e capace di durare per più getti. Come è facile immaginare tutti i casseri delle murature interne ed esterne, trattandosi di una struttura inclinata, sono stati modificati di piano in piano partendo da uno studio progettuale iniziale effettuato con la modellazione degli stessi per l’intero sviluppo in altezza calcolandone spinte e tenute mediante una simulazione al computer delle tensioni presenti. Le murature interne sono cresciute anche loro con un sistema rampante più semplice ma lo allo stesso modo efficace, in questo caso oltre alle suddette difficoltà si aggiungevano quelle provenienti da spazi angusti e limitati compresi tra le due vele esterne ed il ponteggio che seguiva nella crescita la struttura. Il nocciolo interno alle scale a forma variabile è stato realizzato con un ingegnoso cassero realizzato appositamente in acciaio costituito da due centine esterne e due interne chiudibili tramite cerniere e perni capace di una modulabilità che ha consentito di realizzare 4 sezioni tonde differenti e una rettangolare di raccordo a larghezza variabile. Tutti i casseri in negativo delle finestre, delle forometrie, delle scale, dei pianerottoli e delle travi sono stati modellati direttamente in cantiere tramite computer tenendo conto delle tolleranze e quindi disegnati sul multistrato e opportunamente sagomati ed assemblati. Le giunzioni sono state parificate con paste usate in campo automobilistico per la riparazione delle carrozzerie, levigate e dipinte con smalti acrilici al fine di renderle il più possibile invisibili. Le scale elicoidali sono state ricavate mediante uno stampo in polistirene ad alta densità disegnato a computer e tagliato a pantografo rivestito in vetroresina realizzato in tre pezzi e assemblato direttamente in opera piano dopo piano. Ogni getto orizzontale comprendente scale, rampe e pianerottoli è stato inoltre realizzato in opera con la finitura superficiale definitiva tramite lisciatura, spechiettatura con frattazzino e rigatura effettuata su cemento fresco. Tutto ciò è stato possibile grazie alla sinergia che si è venuta a creare tra la le diverse ditte impegnate all’interno del progetto i relativi staff tecnici e la direzione lavori. Nel dettaglio l’Impresa Del Bianco s.r.l. per la realizzazione e la logistica, Calcestruzzi e Italcementi per il calcestruzzo fotocatalitico a base di TX Active. Tra queste ditte una continua programmazione e confronto unita ad una costante presenza sul campo del progettista e direttore dei lavori l’Ing. Lorenzo Saccomano, profusi in un impegno unidirezionale hanno portato alla realizzazione di questa importante opera. Le riunioni effettuate con i tecnici alla fine non si contano, la disponibilità e la professionalità nemmeno, in particolare quella dell’Ing. Saccomano Lorenzo al quale va una menzione speciale di gratitudine è stata fondamentale e strategica per la riuscita. Sin dall’inizio si è creata con lo stesso un’ottima sintonia di lavoro grazie anche ad un’utile e costruttivo confronto che è perdurato per l’intero sviluppo dell’opera in un continuo scambio di pareri ed informazioni tecniche. Una nota per l’impegno agli staff di Italcementi e Calcestruzzi. Le maestranze con le quali ho avuto la fortuna di lavorare: Beniamino (capocantiere) e via di seguito le altre, si sono dimostrate ben all’altezza della situazione assecondando le esigenze, risolvendo problematiche impegnative, superando condizioni fisiche ambientali e climatiche non indifferenti. Il confronto e la collaborazione è stata sempre totale, costruttiva cresciuta sulla base di un rispetto reciproco di una esperienza indubbia ma soprattutto su delle qualità umane indiscusse ritrovabili in principi e uomini di altri tempi; che hanno affrontato il lavoro con passione come fosse una sfida personale da vincere. Ringrazio inoltre Don Giuliano, oltre che per la guida “psicologica”, per la sua umanità, per la sua continua presenza ed interessamento complimentandomi con lui per le sorprendenti capacità tecniche affinate nel corso dell’evolversi dell’opera. Ha saputo con la diplomazia che gli compete anche nei momenti più difficili e delicati distendere gli animi e stemperare le tensioni. A lui il merito di avere fortemente voluto tale opera che grazie alla Amministrazione Comunale ed ad uno stanziamento Regionale è potuta diventare realtà. La ricostruzione del Campanile di Majano è stato un cantiere impegnativo, durato oltre due anni con problematiche legate alla complessità del progetto.
Ing. Sandro Zanin
Impresa Del Bianco - Udine
Scheda tecnica calcestruzzi
Miscele impiegate sul cantiere di Majano
A) Mix a base di cemento i.active TECNO (bianco)
B) Mix a base di cemento i.active TECNO (grigio)
Il prodotto è stato prescritto e venduto Rck 40 XC4 in classe di consistenza che va da S3 (scale, tetti inclinati) a SCC (vele bianche). Vista la distanza degli impianti Calcestruzzi dal cantiere, tutte le miscele sono state progettate e fornite con ritardante di presa (Basf Pozzolith BM).
Mix calcestruzzo bianco
I mix bianchi sono stati prodotti con 5 classi di aggregati provenienti da Carrara (marmo bianco frantumato) e cemento fotocatalitico i.active TECNO di Italcementi.
In base alla stagione (temperatura ambiente) e alla consistenza richiesta, tre sono stati i prodotti messi a punto:
A1) SCC, calcestruzzo autocompattante
Ottenuto mediante due tipi di additivo superfluidificante ad alta efficacia. Non è stato impiegato viscosizzante (AMV) in favore della riuscita estetica del manufatto.
A2) S5, spandimento >55 cm
Si tratta di una consistenza richiesta dall’Impresa di costruzioni per la tenuta non adeguata delle casseforme alla pressione esercitata dal conglomerato SCC. Essenzialmente è la stessa composizione del calcestruzzo autocompattante con una minore quantità di additivo riduttore d’acqua.
A3) S3, per scale interne
In questa parte d’opera Calcestruzzi ha proposto una miscela con diametro ridotto a 8 mm e un additivo a base melamminica aggiunto in cantiere. Questo particolare tipo di additivo garantisce un bassissimo sviluppo di aria inglobata e una reologia del calcestruzzo fresco ideale per la colata in scale armate.
Mix calcestruzzo grigio
I mix grigi sono stati prodotti dallo stabilimento di Udine Beivars per non causare inquinamento di colore con i mix bianchi. Il fornitore di aggregati Carrara ha preparato, su nostra indicazione, un premiscelato con 3 classi di aggregati fini (filler e sabbie) cui è stato aggiunto ghiaino tondo locale e cemento fotocatalitico i.active TECNO di Italcementi.
In base alla consistenza richiesta, due sono stati i prodotti messi a punto:
B1) S5, spandimento >55 cm
L’impostazione del mix è del tutto simile alla mix A2, mutati i componenti come sopra.
B2) S3, per la copertura finale
L’impostazione del mix è del tutto simile alla mix A3, mutati i componenti come sopra, quindi con l’aggiunta di additivo melamminico ma con diametro massimo dell’aggregato pari a 16 mm.
Posizione
Piazza della Chiesa, 733030 Majano (Italia)
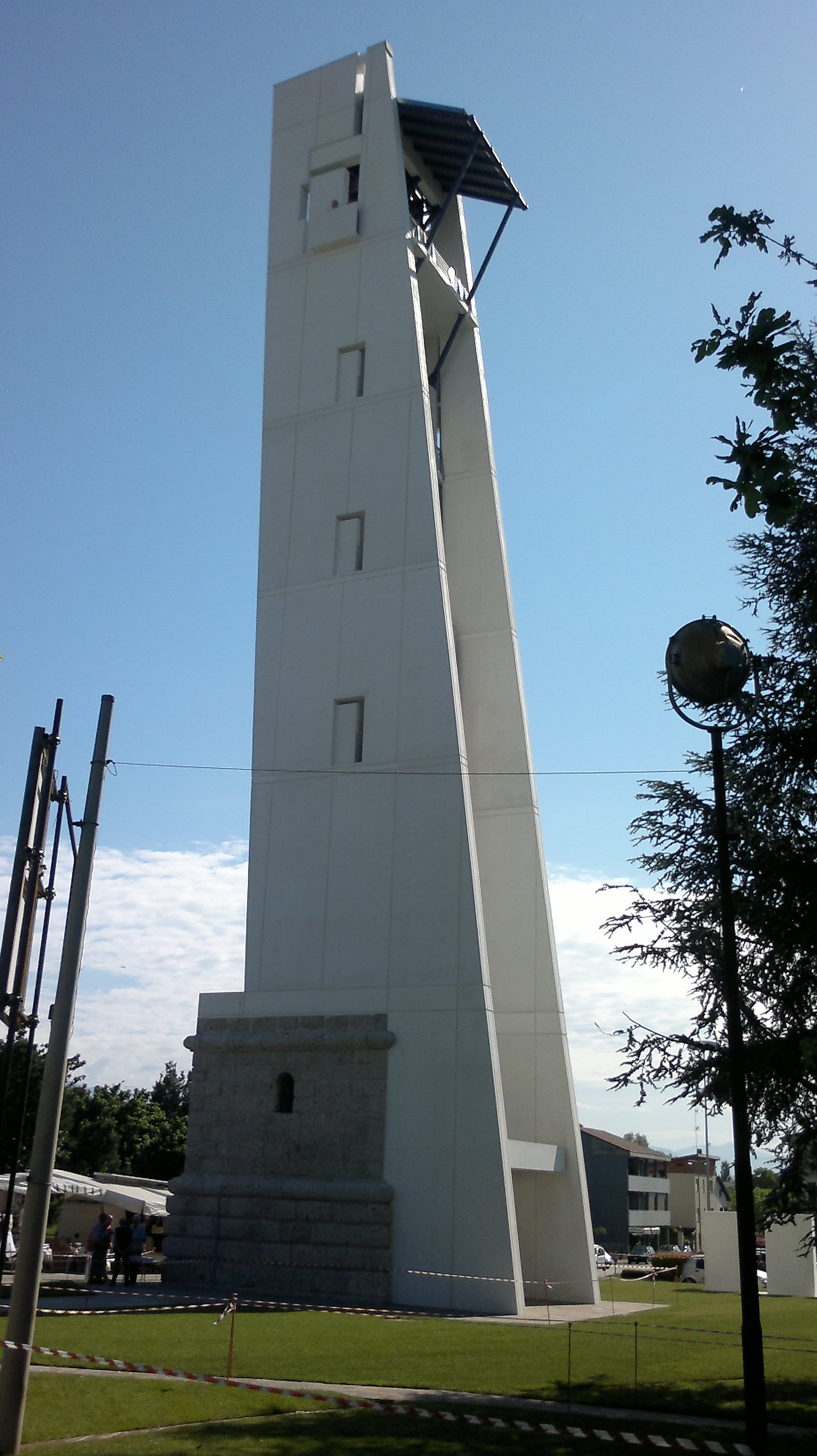
Campanile di Majano (UD).
Italcementi
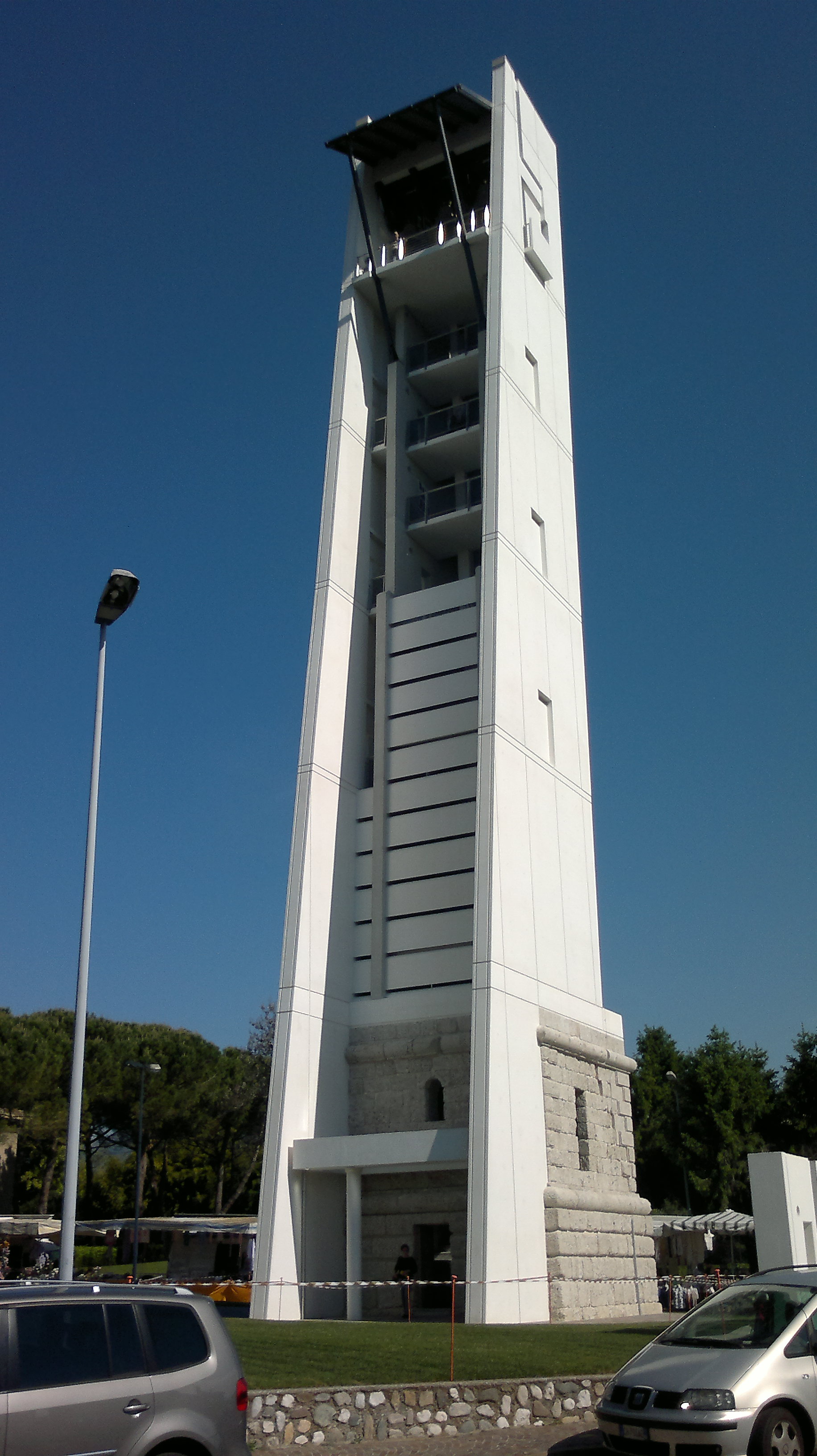
Campanile di Majano (UD).
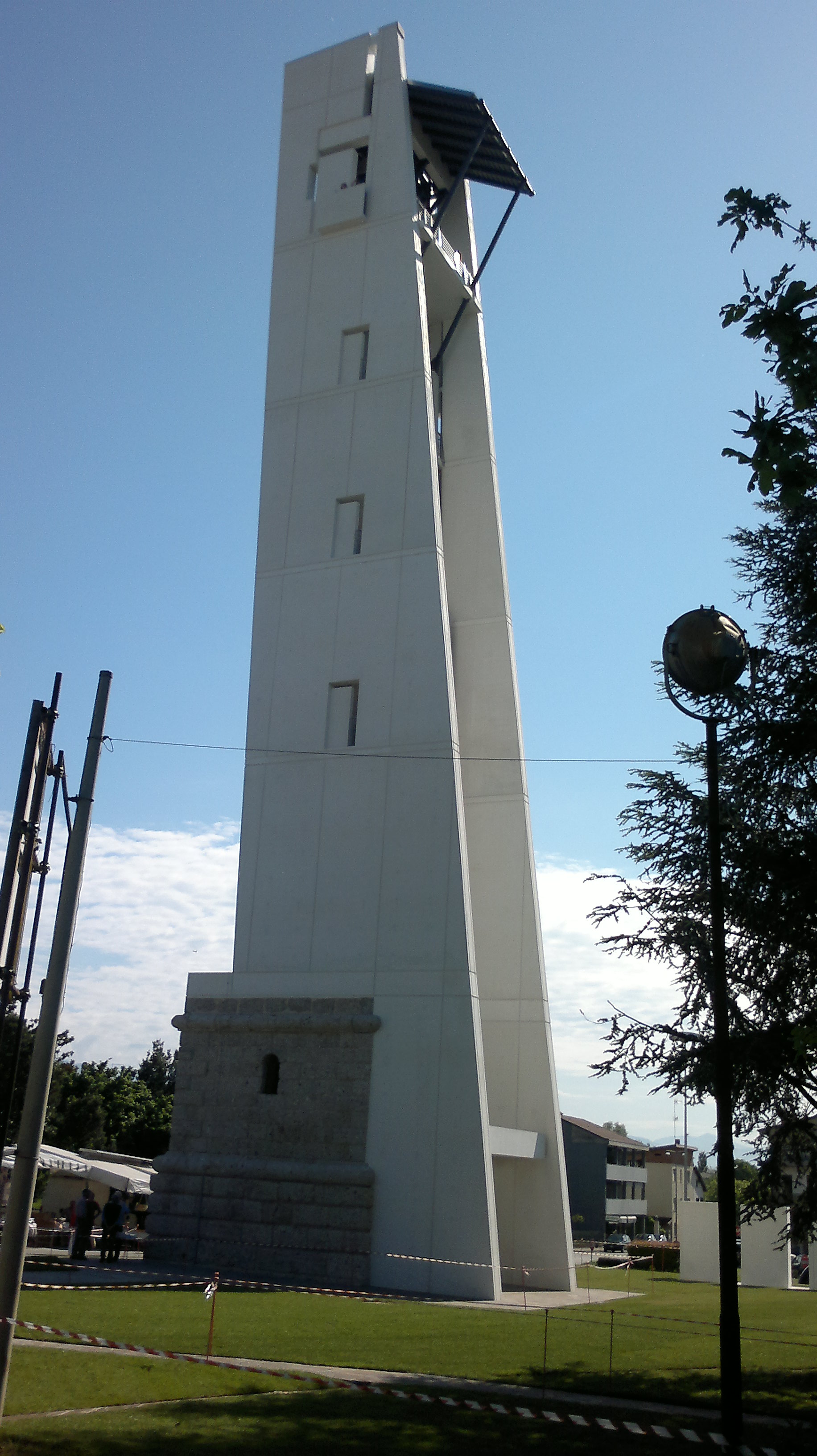
Campanile di Majano (UD).
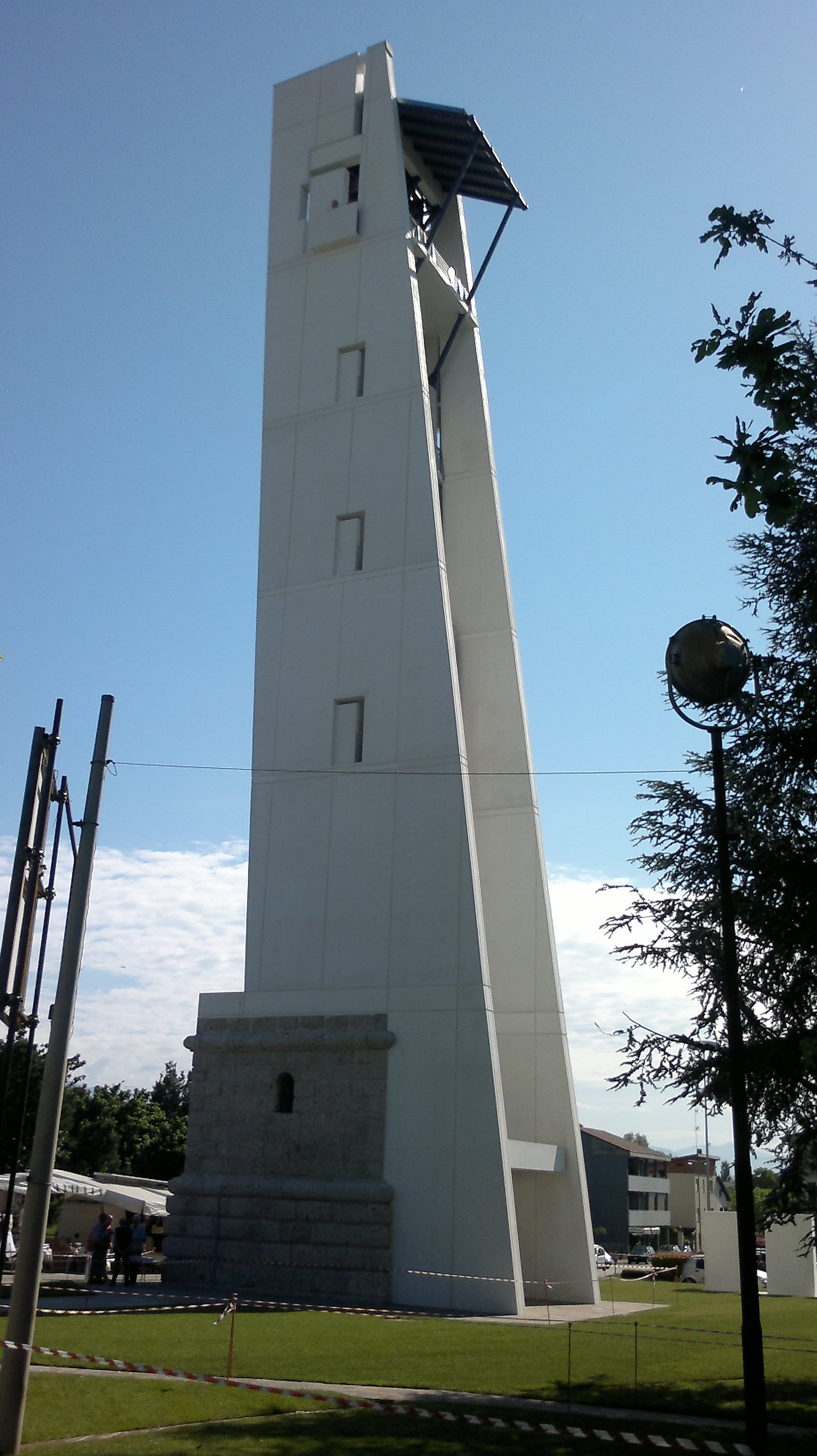
Campanile di Majano (UD).
Italcementi
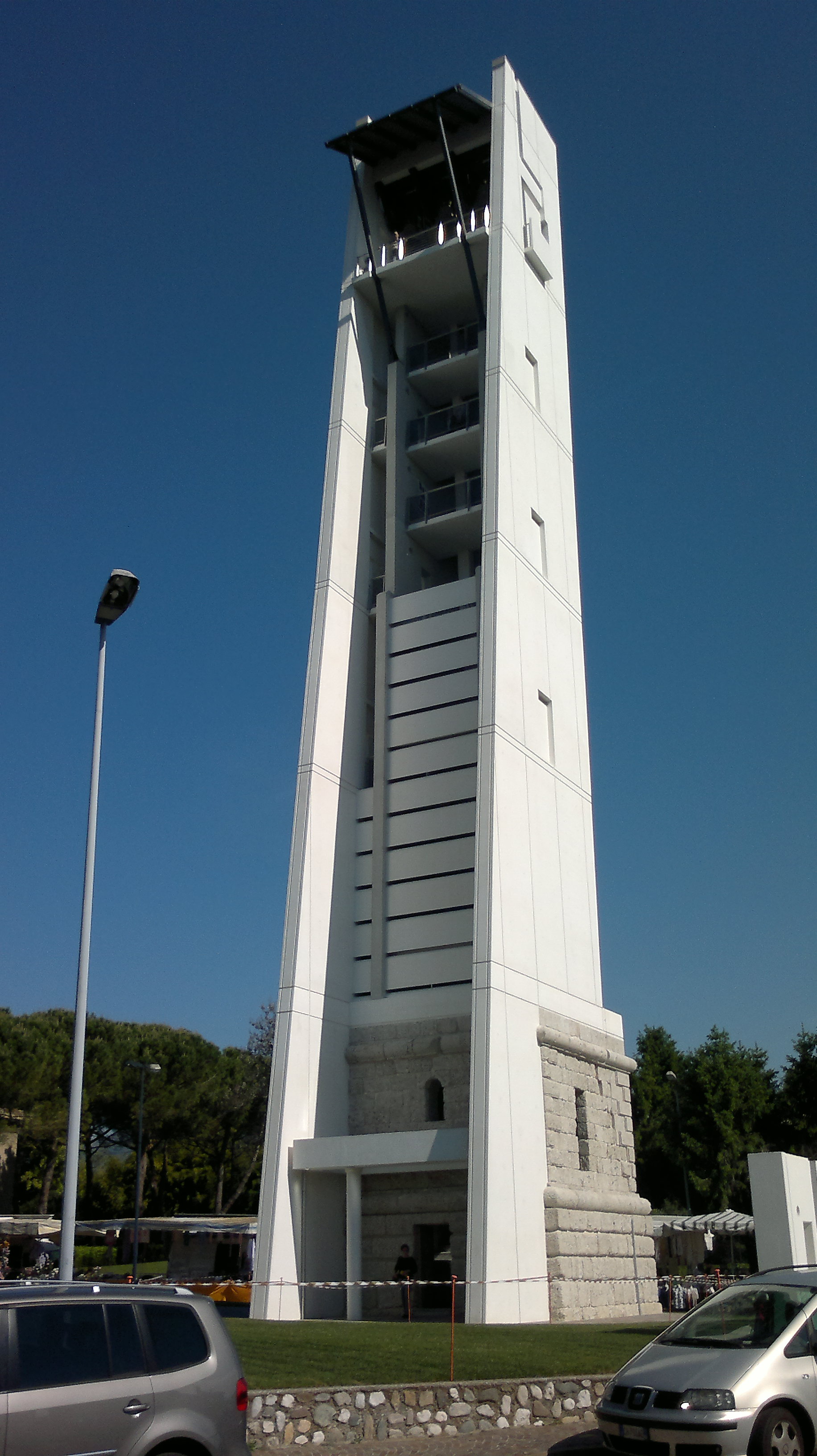
Campanile di Majano (UD).
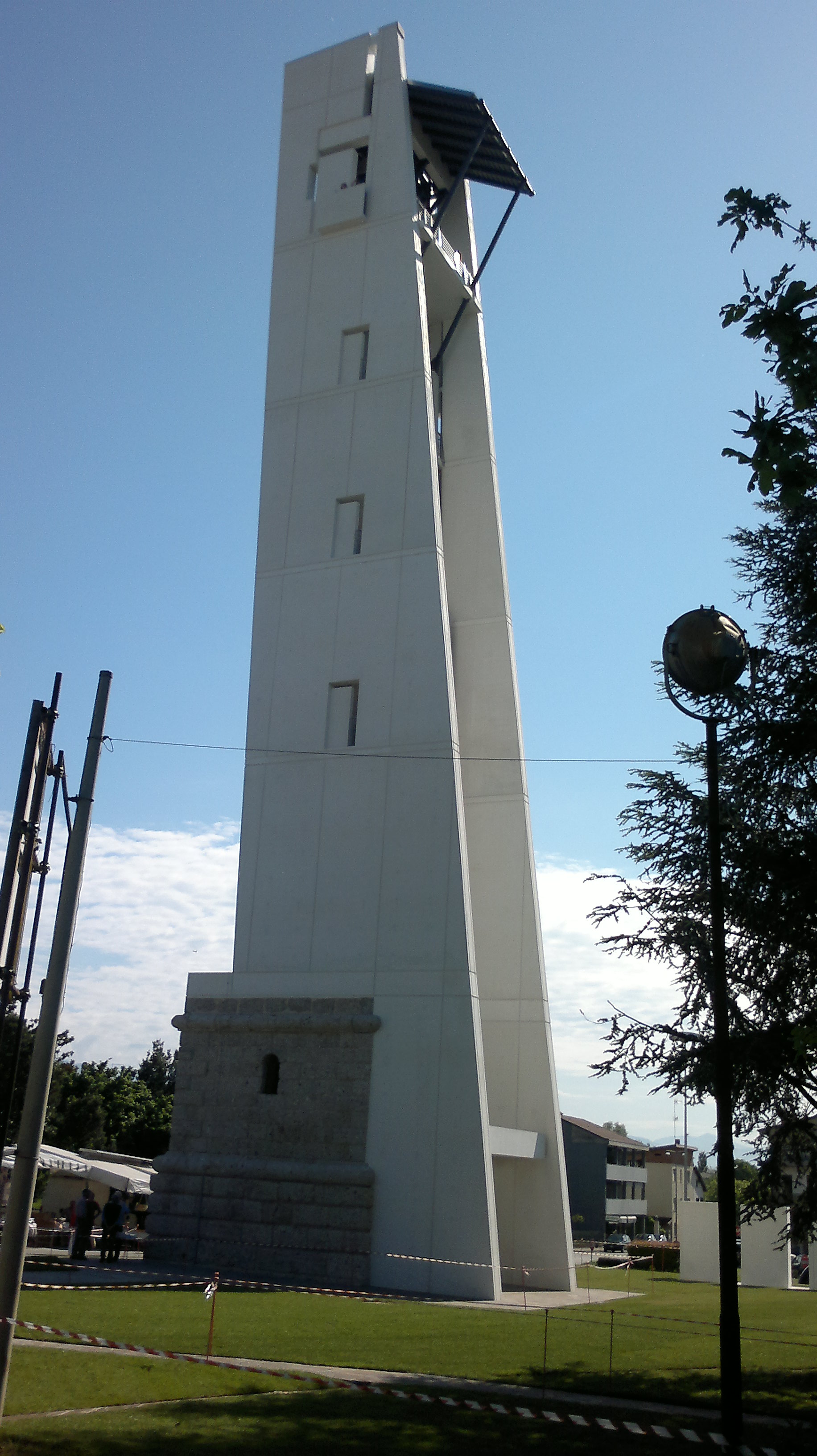
Campanile di Majano (UD).