Prefabbricati Magnetti Building per la sede dell'Azienda Elettronica FM
L’Azienda Elettronica FM è una realtà industriale presente nel mantovano, dalla consolidata esperienza nella progettazione di sistemi elettronici. La necessità di una nuova sede ha portato al progetto, da parte dello Studio AD di Guidizzolo (MN), di un edificio realizzato da Magnetti Building, storica azienda leader nel settore dei prefabbricati in calcestruzzo.
Descrizione dell'edificio
L’edificio, ubicato nella zona industriale di Guidizzolo, ma in prossimità delle zone destinate a verde, è suddiviso in due corpi distinti: il complesso produttivo, a un piano fuori terra, che si sviluppa su un’area di circa 5.500 mq e la palazzina uffici, con spazi direzionali e di rappresentanza, disposta su due piani per oltre 1.700 mq complessivi.
Il primo corpo ha un andamento orizzontale, come suggerito dalla modesta altezza, dai pannelli ad asse orizzontale di colore bianco e dalla pensilina in calcestruzzo, anch’essa bianca e dall’andamento continuo lungo tutto il perimetro.
Il secondo corpo è contraddistinto dalla presenza di un colonnato caratterizzato da pilastri con sezione ogivale, di colore bianco, demandati al sostegno di elementi frangisole e della copertura, anch’essa bianca, realizzata in pannelli in cls a sezione trapezoidale e a profilo sottile. Particolare attenzione è stata posta alla qualità dell’illuminazione naturale all’interno: nel complesso produttivo è stata adottata per la copertura una soluzione a luce orientata con shed, mentre sul perimetro è stata prevista una finestratura continua posta al di sotto della pensilina in calcestruzzo, che ha anche funzione di ombreggiamento.
Nella palazzina uffici, la regolazione della luce è stata invece demandata alla copertura del portico e agli elementi frangisole, che sono stati previsti all’esterno del colonnato, sostenuti dai pilastri a sezione ogivale.
Sulla copertura della porzione produttiva, realizzata con elementi alari in c.a.p. aventi luce di circa 20 m, prefiniti in stabilimento e distanziati da elementi macroshed, è previsto un impianto fotovoltaico a brevetto di Elettronica FM, in cui ogni singolo pannello, al fine di incrementarne l’efficienza, è dotato di un micro inverter. L’adozione di elementi di copertura prefiniti, ovvero di prefabbricazione estesa anche a parte delle finiture, applicate già in stabilimento, fornisce notevoli benefici in termini di costanza qualitativa dei processi produttivi e nella riduzione dei tempi di cantiere.
L’esigenza di un’estesa area coperta per le operazioni di carico è stata risolta mediante la creazione di un portico interno all’edificio produttivo e la realizzazione di una pensilina in c.a.p., finalizzata a mantenere l’omogeneità architettonica con gli altri prospetti dell’edificio.
Scelte progettuali e problematiche esecutive
Da parte di Magnetti Building, La scelta della prefabbricazione degli elementi strutturali e di tamponamento è stata dettata dalla necessità di contenere i costi ed i tempi di cantiere, dall’impegno statico di alcune soluzioni e, infine, per l’esigenza di ottenere uno standard qualitativo elevato delle superfici bianche a vista, meglio ottenibile tramite un processo produttivo
industrializzato. L’elemento più peculiare e caratterizzante dell’intervento appare il colonnato della palazzina uffici. Esso è caratterizzato da pilastri a sezione ogivale che sorreggono elementi di solaio con appoggio puntuale, senza la presenza di travi.
Dal punto di vista progettuale ciò ha comportato la necessità di ridefinire lo schema strutturale dei solai, adottando per essi un appoggio continuo su travi poste lungo i prospetti (poste al di sopra dei serramenti e mascherate dai pannelli della palazzina) ed appoggio puntuale in corrispondenza dei pilastri del colonnato.
Tale schema ha reso necessaria l’adozione di uno schema ad armatura incrociata. Ai fini delle valutazioni dello stato tensionale e del dimensionamento delle armature, data la particolarità delle modalità di appoggio dei solai, si è utilizzato un modello semplificato ad elementi finiti.L’esigenza di ottenere uno spessore ridotto in corrispondenza del bordo a vista dei solai, all’esterno del colonnato, ha poi comportato l’adozione di elementi solaio a sezione trapezoidale. Notevole attenzione, in fase progettuale, è stata posta nello studio delle modalità di movimentazione dei pilastri e dei solai del colonnato nelle varie fasi di sformo, stoccaggio, trasporto e montaggio, anche al fine di evitare danni estetici alle superfici visibili dei manufatti.
Dal punto di vista produttivo, la realizzazione dei solai del colonnato ha comportato la messa a punto di specifici dettagli costruttivi, oltre ad una fase di prototipazione per l’ottimizzazione dell’aspetto delle superfici a vista.La particolare sezione è stata ottenuta mediante imbottiture delle casseforme, partendo da un tradizionale pannello a sezione rettangolare. Gli inserti in acciaio finalizzati al vincolo dei pannelli solaio alla trave e al pilastro sono stati progettati e realizzati appositamente. Per i pilastri si è invece reso necessario l'approvvigionamento di casseri ad hoc. Le armature e i dettagli costruttivi dei manufatti sono stati progettati in accordo alle Norme Tecniche delle Costruzioni [1] vigenti (NTC 2008). La sezione ogivale dei manufatti è stata adottata solamente per le parti a vista fuori terra, mentre alla base dei pilastri, nel tratto inghisato nel pozzetto di fondazione, è stata mantenuta la sezione rettangolare, con dimensioni cm 75x50, al fine di stabilizzare il manufatto nelle fasi di stoccaggio e trasporto. All’interno dei pilastri a sezione ogivale sono state predisposte canalizzazioni finalizzate al passaggio dei cavi elettrici dei pannelli fotovoltaici previsti.
L'edificio nasce con l'esigenza di coniugare gli aspetti architettonici con quelli della massima efficienza energetica. Sono stati utilizzati pannelli a taglio termico con isolante da 14 cm ed eliminati tutti i ponti termici con la realizzazione di cordoli isolati nei punti di connessione tra le due tipologie di pannello. I frangisole fotovoltaici sono stati studiati per garantire gli apporti solari gratuiti nei mesi invernali e l'ombreggiamento nei mesi estivi.
Impiantisticamente è stata progettata una soluzione con sistema Vrf permettendo di sfruttare al massimo la produzione fotovoltaica garantendo la temperatura ideale in ogni ambiente con la massima autonomia di gestione. L'adozione di canali microforati per il reparto produttivo permette di evitare flussi d'aria diretta. È stata prevista anche per i pilastri la realizzazione di prototipi, finalizzati sia alla definizione del mix design del calcestruzzo che delle modalità di getto e di finitura delle varie superfici, in particolare quella superiore (non controcassero). Sono stati provati vari impasti e diversi sistemi di getto e finitura, fino a pervenire alla definizione delle modalità di produzione. Il montaggio della strutture prefabbricate dell’edificio è stato ultimato nel mese di aprile 2018.
Materiali impiegati
Per gli elementi prefabbricati che definiscono l’involucro (pannelli, pensiline, colonne e cornicione del complesso), la scelta architettonica è stata quella di adottare il colore bianco, a contrasto con il verde circostante.
Al fine di garantire una migliore pulizia nel tempo delle superfici a vista, per la realizzazione dei manufatti sono stati previsti calcestruzzi realizzati con cemento bianco fotocatalitico i.active TECNO BIANCO 42.5 di Italcementi. Il cemento utilizzato (contenente biossido di titanio) è caratterizzato dal possedere un’attività fotocatalitica che si sviluppa grazie alla specifica formulazione: in presenza di luce e aria fa sì che si attivi un processo ossidativo che porta alla decomposizione di sostanze organiche e inorganiche inquinanti quando queste vengono a contatto con la superficie del manufatto cementizio. Di conseguenza, l’impiego di questa tipologia di cemento conferisce ai manufatti la capacità:
• disinquinante, in grado di purificare l’aria ottenendo una concreta riduzione delle sostanze organiche e inorganiche provenienti dell’inquinamento atmosferico, con funzione ecosostenibile;
• di conservare le caratteristiche estetiche dei manufatti nel tempo, permettendo di avere superfici più pulite.
Negli edifici industriali ed artigianali la prefabbricazione è lo standard di mercato e può essere utilmente estesa anche a parte delle finiture (ad esempio con elementi di copertura prefiniti) per ridurre tempi e costi. L’industrializzazione del processo garantisce costanza produttiva con elevata qualità. L’edificio in esempio mostra come la prefabbricazione possa essere utilizzata anche in presenza di soluzioni architettoniche non standard. L’approccio progettuale, che non può comunque prescindere dall’impiego di tipologie standard ove ciò è possibile, può prevedere la specializzazione o la progettazione ad hoc di parte dei componenti, al fine di realizzare soluzioni particolari o, come nel caso specifico, di ricercato pregio architettonico.
Posizione
Via Leonardo da Vinci, 2746040 Guidizzolo (Italia)
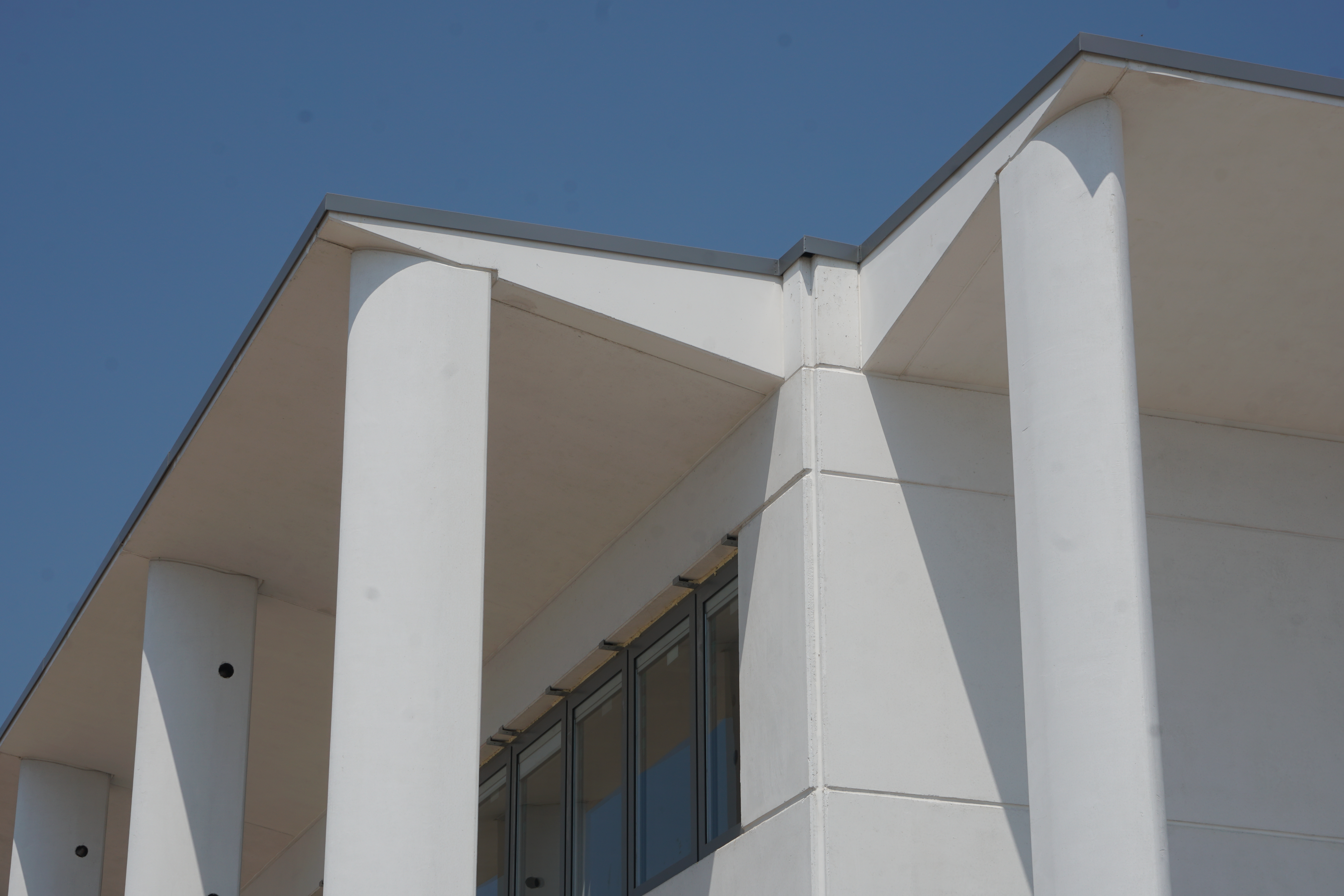
Edificio Magnetti.
Magnetti Prefabbricati
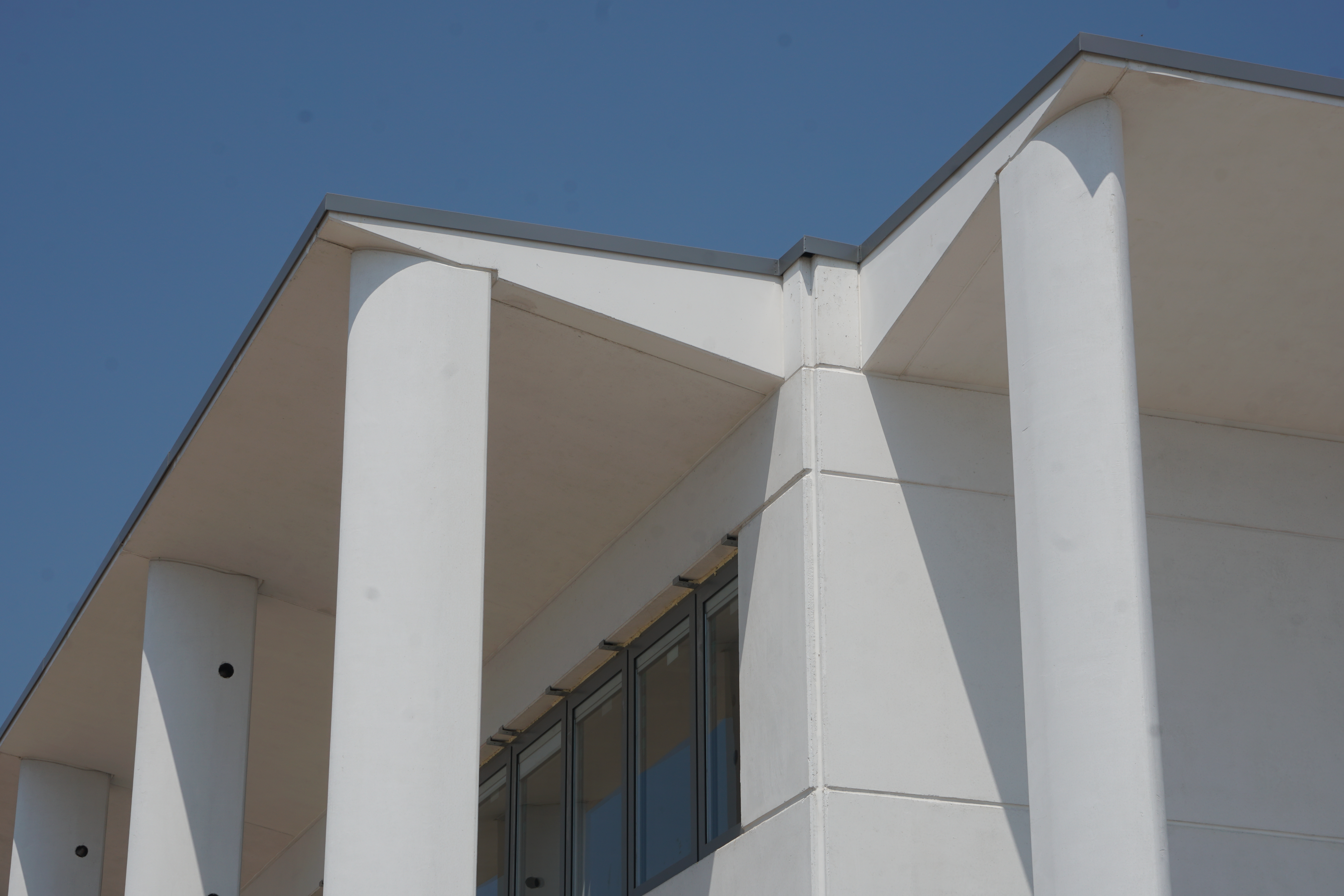
Edificio Magnetti.
Magnetti Prefabbricati